新浪汽车讯:奥迪A6这款产品是最早进入中国的合资豪华轿车,经过在中国4代车型的发展,最新的第七代产品已经量产,并将在不久后上市。作为驾驶过奥迪在华4代A6的人,对这款产品总有特殊的感情,也对它的发展十分熟悉。记得在05年第一次接触第6代车型时,对车身结构和动力总成飞跃式的进化有极其深刻的印象。A6这个车款在A8诞生之后的发展中一直受到A8的影响,每一代新A6上都或多或少的留有A8的影子,第七代产品则属于受影响比较大的车款之一。除了高级别车型的影响外,模块化战略的影响也在这代车型上体现,作为最新款的奥迪车,这代A6L几乎包含了所有奥迪最新的技术模块,例如:环保直喷发动机、S tronic传动系统、钢铝复合车身、前轴前移、多连杆铝制悬挂、新一代MMI多媒体交互兼容后排多媒体系统、LED照明系统、ACC自适应巡航、预碰撞安全系统、带行人识别的夜视系统等等。为了让网友更好的了解第七代A6L的技术特性,本文将对这些新技术进行一一解读。
-------------------------------------------------------------------
-------------------------------------------------------------------
一、车身和悬挂:
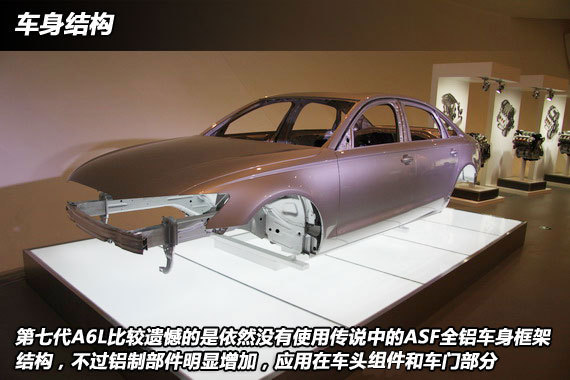
奥迪一直是轻量化车身的倡导和积极推动者,其ASF全铝车身在业内独树一帜,在第七代A6没有上市之前就有传言说该款车型将采用全铝车身,但事实证明这仅仅是传言,就像第六代车型那时一样。也许是中国的铝结构件制造能力拖了后腿也可能是出于成本考虑,这代车型没有采用全铝车身。但是面对竞争对手的轻量化压力,这代A6L采用了大量的铝制部件,同时这些部件已经实现国产。也许中国的铝制车身之路还需一步步的走。
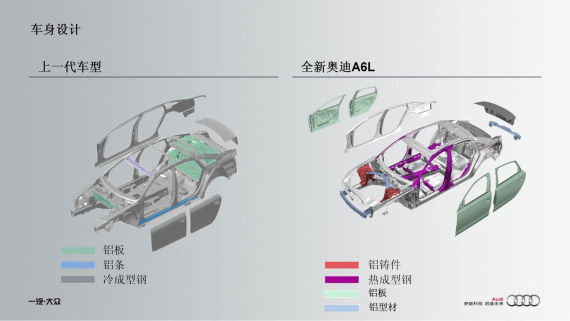
从车身材料图中可以看到,与第六代铝制引擎盖、翼子板都未能装配在国内车型上相比,这代的铝制部件用量可以用飞跃来形容。车门、前减震器支架、内板都采用铝制部件。
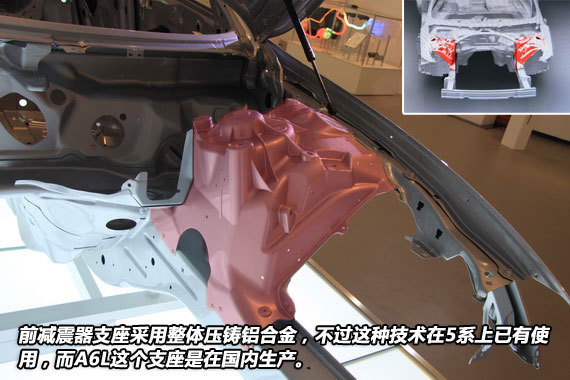
前减震器支座是全车最大的铝制部件,其实这种结构在宝马5系上也有应用。A6L的这个部件为全铝压铸,通过一个零件取代了原来多个钢制部件拼焊成的减震器支架,对于前驱车来说有非常重要的减轻车头重量的作用。
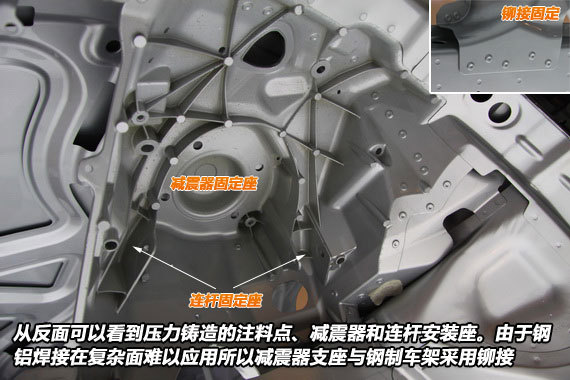
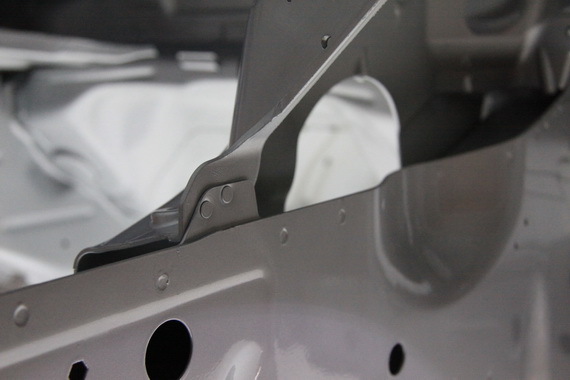
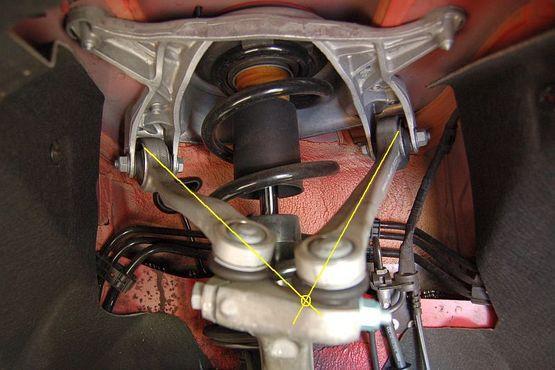
由于铝材和钢材之间目前只有采用激光焊接的方式才能连接,因此像前减震器支座这种大型部件则需要通过铆接的方式和钢制的前纵梁以及上边梁连接,但是这种连接方式难以避免自稳性差的薄钢板在铆接时产生变形。图中看到的这一个大型的铝制部件同时集成了减震器固定座和前悬挂两根上连杆固定座,较少的零件对降低成本和减少制造工序都有好处。从图中可以看出,铝材由于重量轻所以可以增厚使用,3mm厚的部件几乎不可能使用钢材,因此就材料本身的稳固性铝材具有明显优势。
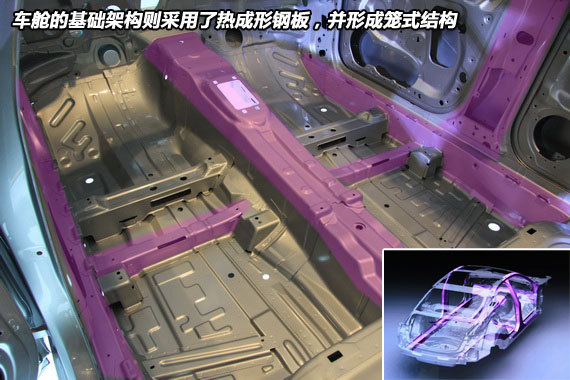
而在车身架构部分,A6L仍然使用了传统设计,只是在高强度的热成形钢板的用量上有很大提升。车舱结构的中央通道、A、B柱、门槛梁和横向加强筋都使用了热成形钢板加固。
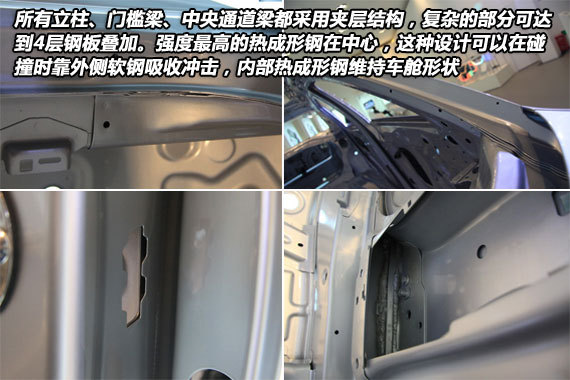
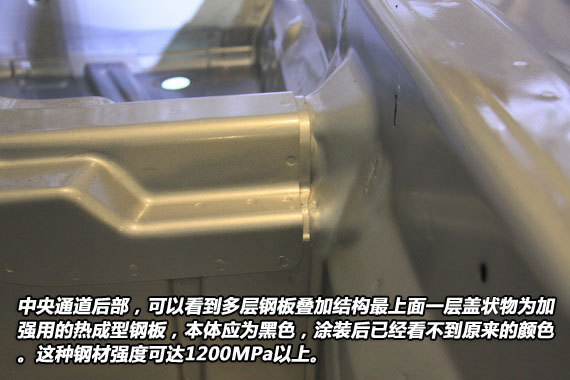
大部分的梁结构都是多层复合结构,由表层软钢、双相钢、诱导相变塑性钢和热成形钢拼焊而成,由外至内、由软至硬。其中强度最高的夹在中心使用的热成形钢。
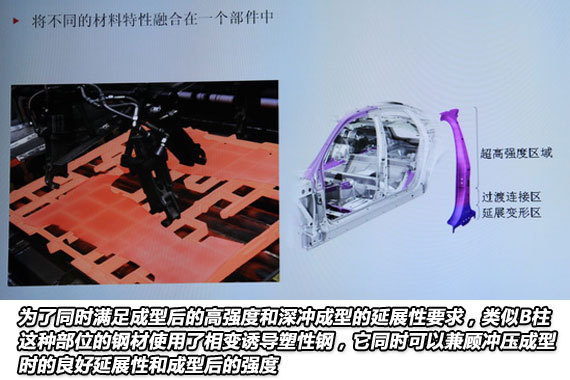
在B柱这种既需要深冲成拥有垂直厚度又在碰撞中面临极大压力的部件使用了诱导相变塑性钢,这种钢材是目前高技术钢种的代表,在制造这种钢材时通过局部调质使其在冲压时拥有良好的延展成型性,不会在加工成型中开裂(加工时表现出柔软的特性),同时又保证热处理成型后在常温下强度更高,在碰撞中能保持其形状(成型后表现出坚硬的特性)。
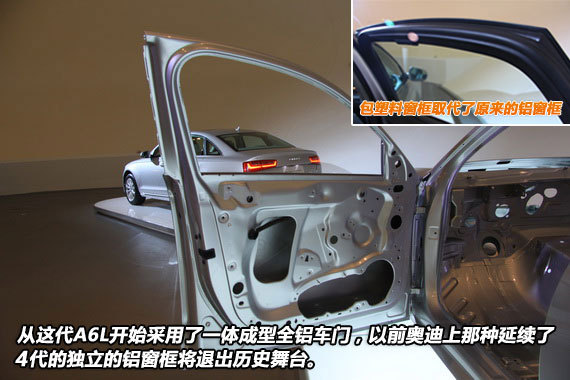
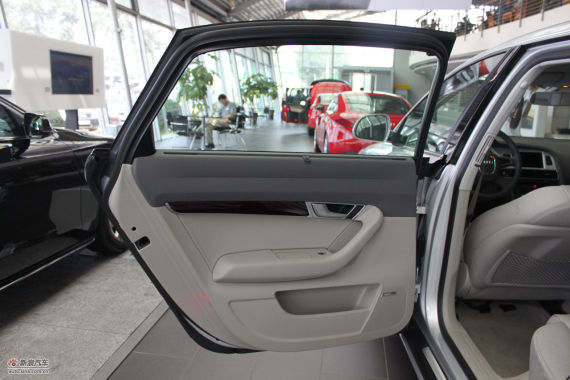
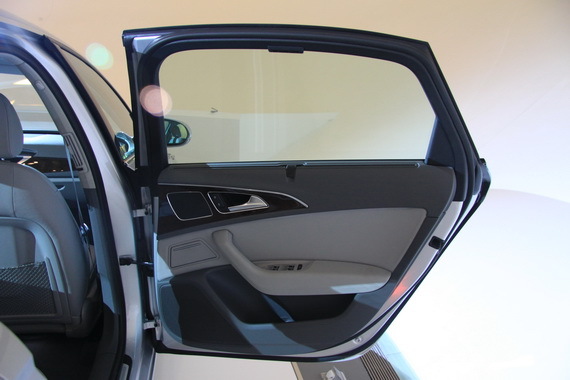
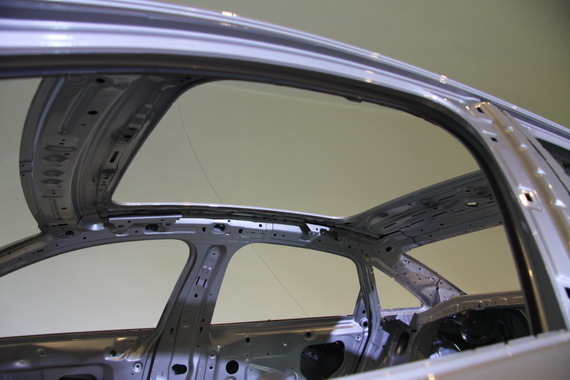
除了前减震器支架外,这代A6L的车门采用了全铝结构,就白车身而言,车门手感非常轻,因此在内部安装再多的附属机构都不会造成开关车门吃力的现象。不过前四代车型中我最喜欢的独立铝制窗框将再也看不见了,因为本代车型的窗框和内门板整合到了一起,也是减少零件数量的设计。
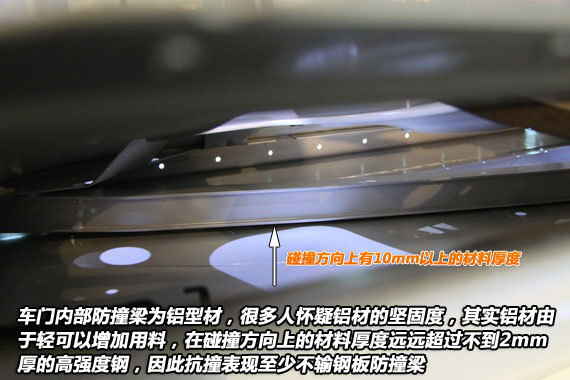
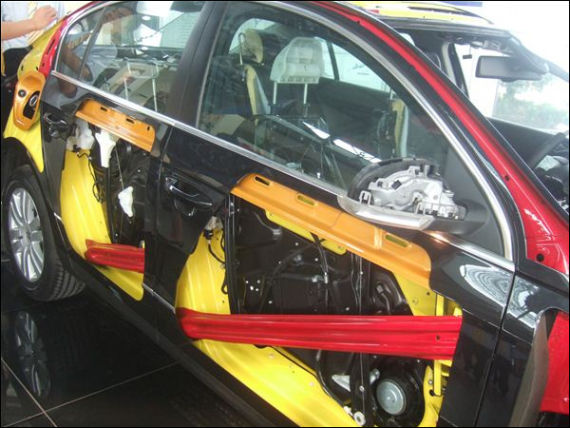
全铝车门的防撞梁也采用铝材,为“工”字型铝合金型材,由于材料本身很轻,所以可以加厚使用,在碰撞方向上达到了将近10mm以上的厚度。与传统的冲压高强度钢防撞梁相比毫不逊色,冲压的钢制防撞梁依靠冲压出来的凸起加强筋承受撞击力,其撞击方向的厚度不过10mm。另外薄板冲压结构非常依赖其形状,且能容忍的变形量很小,一旦变形量超过设计允许量导致受力结构崩塌,那么再高强度的钢板也没了用处。