五、精密加工技术
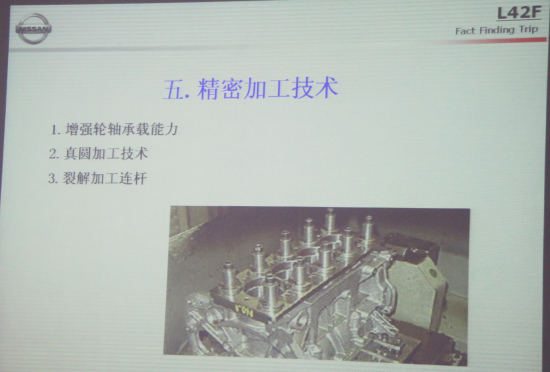
真圆加工工艺
真圆加工是 F1 赛车发动机的加工工艺,日产首次将它应用在普通民用车上,真圆加工可以确保日产的发动机气缸内径相对于其他普通发动机更圆,在发动机运行过程中活塞环与气缸的摩擦更加均匀, 配合间隙更加精密,可有效延长发动机的使用寿命。
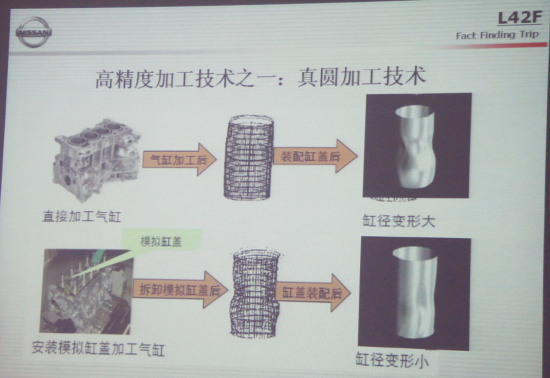
普通发动机是缸筒与缸盖分别单独加工而成。组装发动机缸盖时,必须旋紧缸盖螺丝,此时缸筒会发生变形失圆,发动机运行时,活塞环与缸筒壁摩擦阻力增加,密封性能下降,造成磨合期磨损量大,磨合期油耗增加,如果变形量过大,活塞环还会将缸筒内壁的抗磨涂层磨穿,这时磨损将无法控制,使发动机寿命严重缩短。
真圆加工是在加工发动机缸筒时,将一个模拟缸盖以组装发动机相同的力矩固定在缸体上,然后再加工缸筒内径,缸筒加工完毕再将模拟缸盖拆掉,拆掉缸盖时,缸体的张力会使缸筒变形,但是在安装标准缸盖后,又恢复了缸筒的圆度。
真圆加工使缸筒与活塞环的配合间隙更小,可使用低张力的活塞环及低粘度的机油,即可达到密封要求,保持气缸压力,所以日产系列发动机由于精密度的提升,全部可以使用低粘度的润滑油(5W30),低粘度润滑油有以下优势:流动快、散热好、积碳少、燃油消耗低、寒冷地区启动快,液压系统能快速进入工作状态。
连杆裂体加工工艺
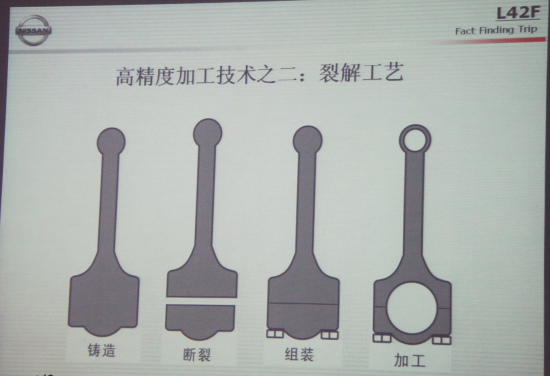
普通发动机连杆的大头部分(与曲轴相连的地方)。一般是分为两个半圆进行加工,加工后组装在 一起,这种方式尽管在加工时尽管加工精度很高,但是用螺柱和螺母扭紧后组装在一起后。会因受扭紧力的影响而产生局部变形,使连杆轴瓦与曲轴之间摩擦力阻力增大,磨合期磨损严重,油耗增加。 东风日产VQ系列发动机的连杆的大头部分在模拟环境下一起加工,经过开裂处理的连杆是 整体生产的,开裂过程产生的不均匀表面的配合产生了非常精确的接口。两个部分在断裂后重新连接, 使用防松脱镙栓来紧固(代替螺丝和螺母),螺栓的拧紧采用进口定值扭矩扳手及扭矩转角法分多步进行拧紧;再加工大头圆孔,这样就保证了连杆大头孔的圆度, 集成铸造的连杆比传统连杆的重量轻,而且通过裂体加工新工艺能确保连接面的精密度。
六、精密控制技术

微粒化喷油嘴
发动机每个气缸配有一个喷油嘴,喷油嘴有两种安装方式,一种为进气管喷射,另一种为缸内喷 射,由于缸内温度较高,缸内喷射对喷嘴材质要求较高,缸内直喷可配合分层燃烧技术,可达到很好 的节油效果,但由于国内汽油质量较差,烯烃含量较高,在高温环境下易产生胶质堵塞喷嘴,所以大 多数汽车厂商采用进气管喷射。
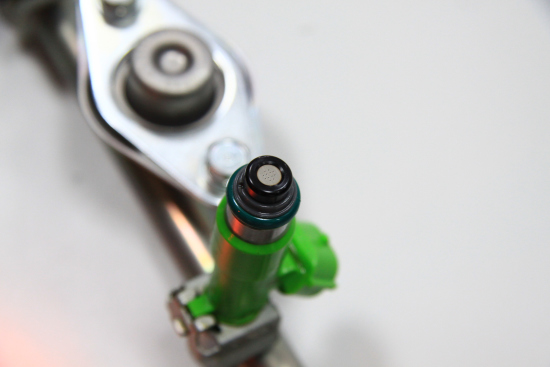
传统的每个喷油嘴为4-8 孔的设计,其喷油颗粒较大,燃烧不完全,造成油耗上升,混合气浓度较大,还易在气门背面造成积碳,积碳会增加进气阻力,使进气气流改变方向,形成乱流,影响油气混合,结果使油耗上升,影响三元催化器使用寿命,东风日产的全系列车型全部配备了微粒化喷油嘴,每个喷油嘴12 喷孔(内径 130 微米),传统喷嘴为4 孔(内径 250 微米),喷出的燃油粒径缩小约40%。