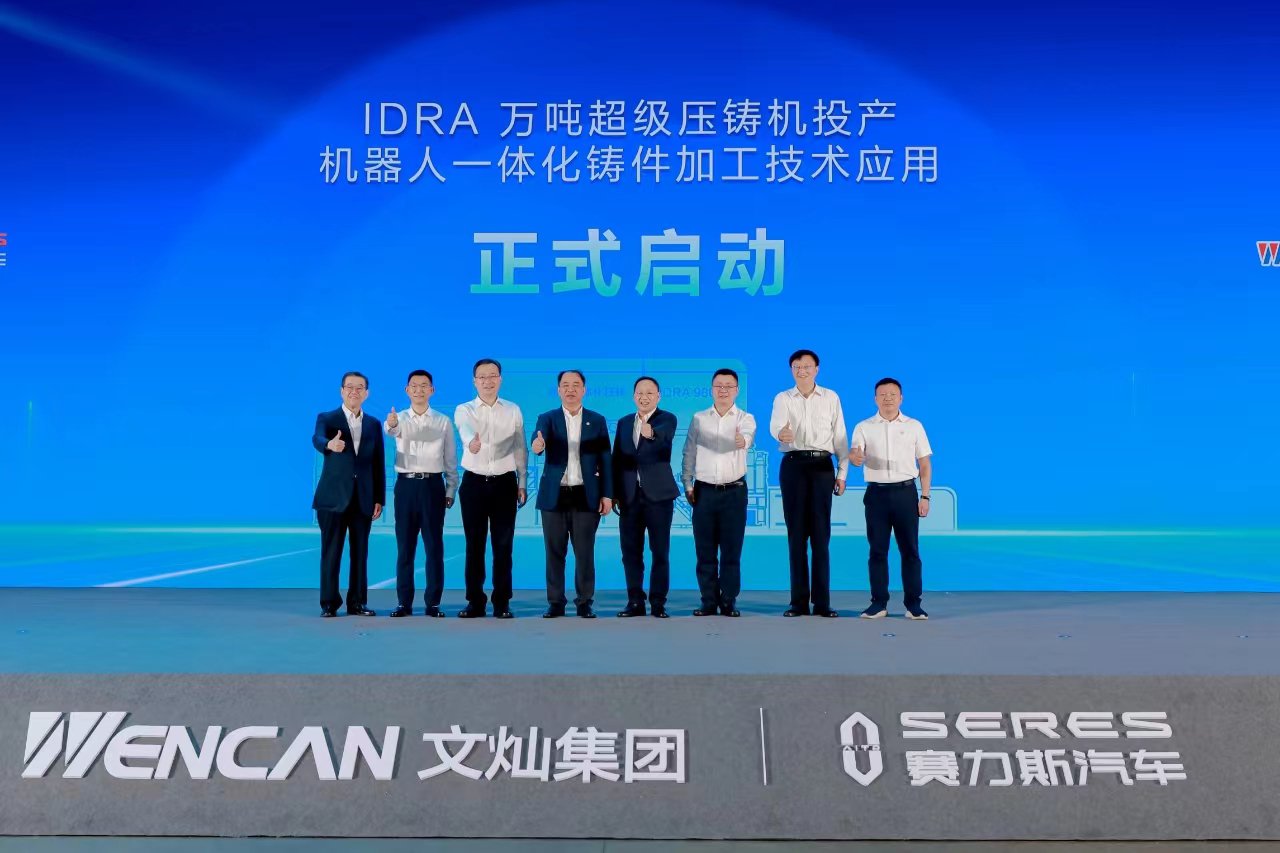
2024年6月28日,赛力斯汽车联合文灿集团举办IDRA万吨超级压铸机投产机器人一体化铸件加工技术应用启动仪式,宣布IDRA万吨超级智能压铸单元正式投产应用,并将首创应用上海发那科自主研发的高精度机器人加工技术。活动现场,重庆市经信委、两江新区区委领导代表,赛力斯集团董事长(创始人)张兴海,文灿集团董事长唐杰雄等多位领导莅临出席,共同见证了这一重要时刻。

高端的产品来自高端的制造,高端的制造需要高端的工艺技术。IDRA万吨超级压铸机的投产应用,树立了汽车行业智能制造新标杆,将推动产业向更高端、智能、集成、集聚、高效的前景进化。张兴海表示:“即将投产的万吨超级智能压铸单元,是目前全球首台、全球最大的两板式压铸单元,这是我们多年来追求汽车轻量化、追求环保绿色的结果,也是赛力斯汽车在重庆‘33618’战略下推行集成化、集聚化‘两化’工程的结果,能够满足用户日益提升的智慧出行体验需求,将让汽车更安全,让用户更自豪。”
汽车的一体化压铸工艺通过集成化制造,能够做到汽车轻量化、节约成本、缩短供应链、提升制造规模等,实现了对传统汽车制造工艺的革新。赛力斯汽车作为技术科技型企业,始终坚持智电融合发展道路,正在依托研发与智能制造实力,深刻诠释“传统豪华+科技豪华”的“新豪华”概念,做到智慧重塑豪华,引领行业技术和智能制造的创新发展。文灿作为国内领先的压铸设备制造商,历经二十余年的发展,在汽车铸造零部件领域已积累良好的信誉和独有的品牌优势,更率先在汽车大型一体化结构件领域获得客户定点、量产,成为一体化压铸领先者。
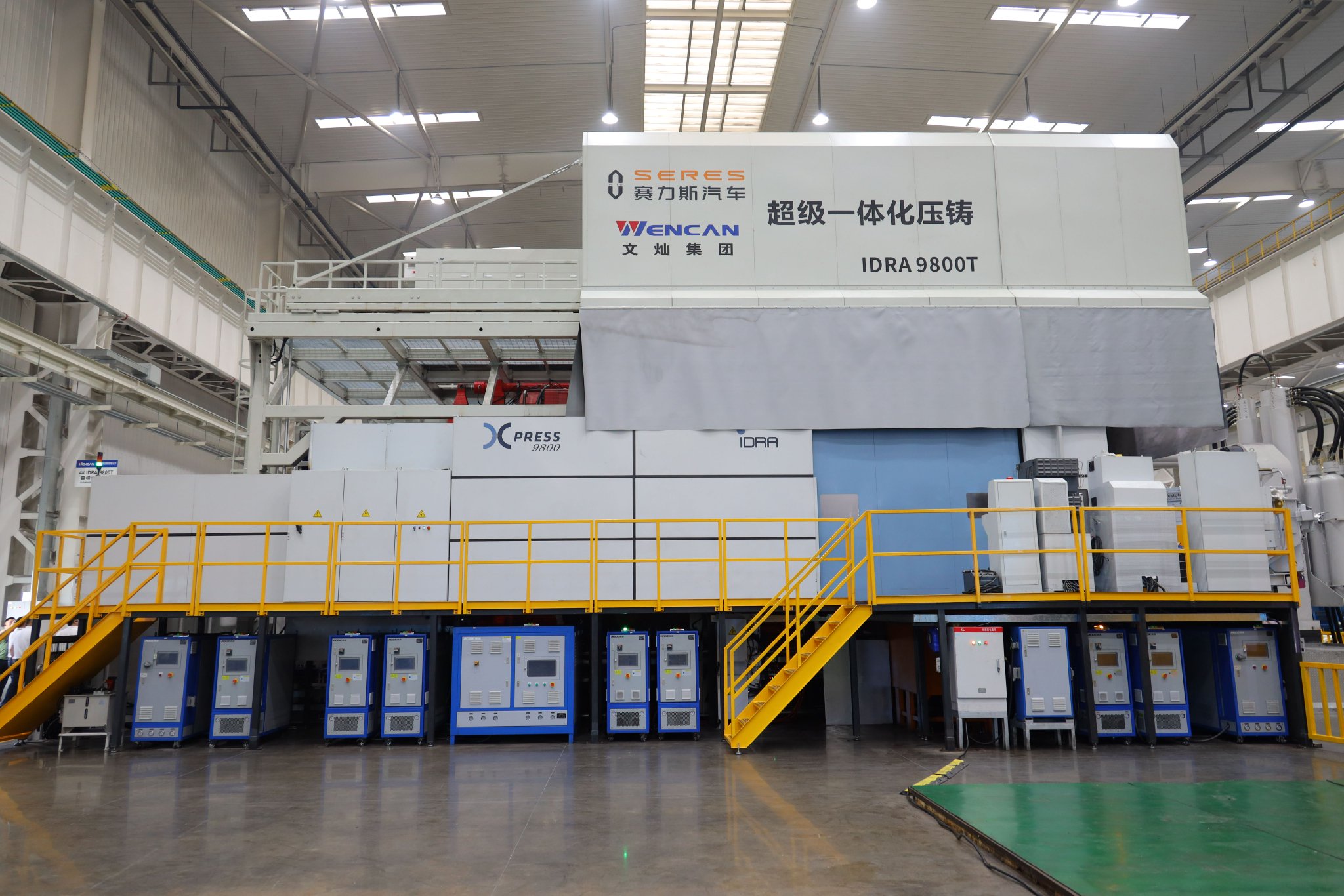
此次双方合作投产应用的IDRA万吨超级智能压铸单元,采用了先进的压铸技术和智能化控制系统,能够通过高精度、高效率的压铸生产,大幅提高生产效率、降低生产成本,增强整车的结构强度和稳定性。赛力斯汽车还宣布将首创应用上海发那科自主研发的高精度机器人大型铣削加工技术,进行一体化大铸件的加工、升级,通过硬件机械结构与软件控制方面的双重优化,实现加工精度、加工刚性、加工速度的高效提升。
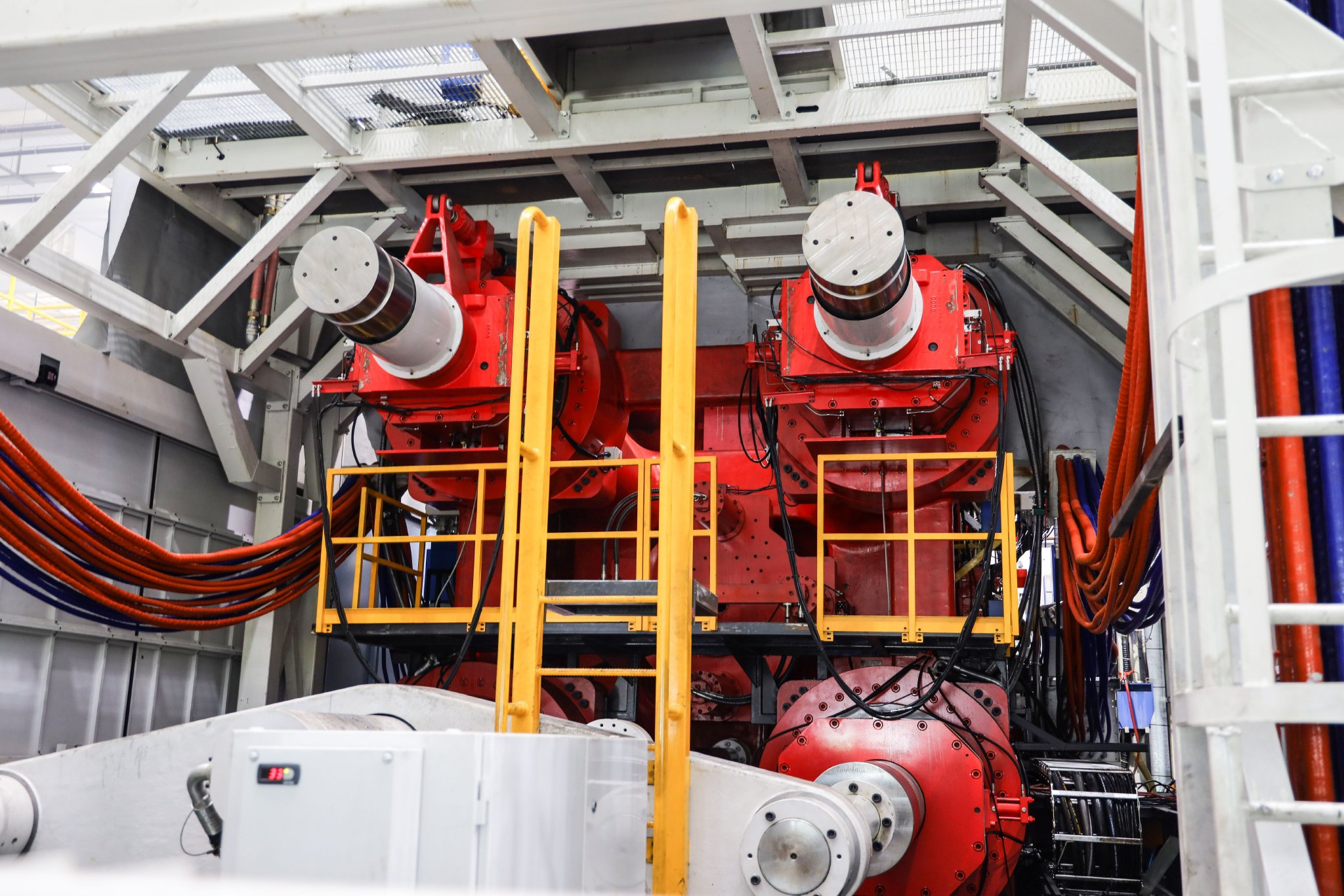
越来越多的车企采用了大压铸车身技术,那么这种新造车工艺有什么优势呢?对于车企来说,能大大提升生产效率。一体化压铸技术通过将多个零件整合为单一大型部件,减少了组装工序,显著提高了生产效率。其次是降低生产成本,由于减少了工序和人工,一体化压铸技术有助于降低制造成本。以问界M9(配置|询价)为例,压铸车身部件使零件集成度提升95%,焊点/连接点数量减少70%,车身扭转刚性提升23%以上。
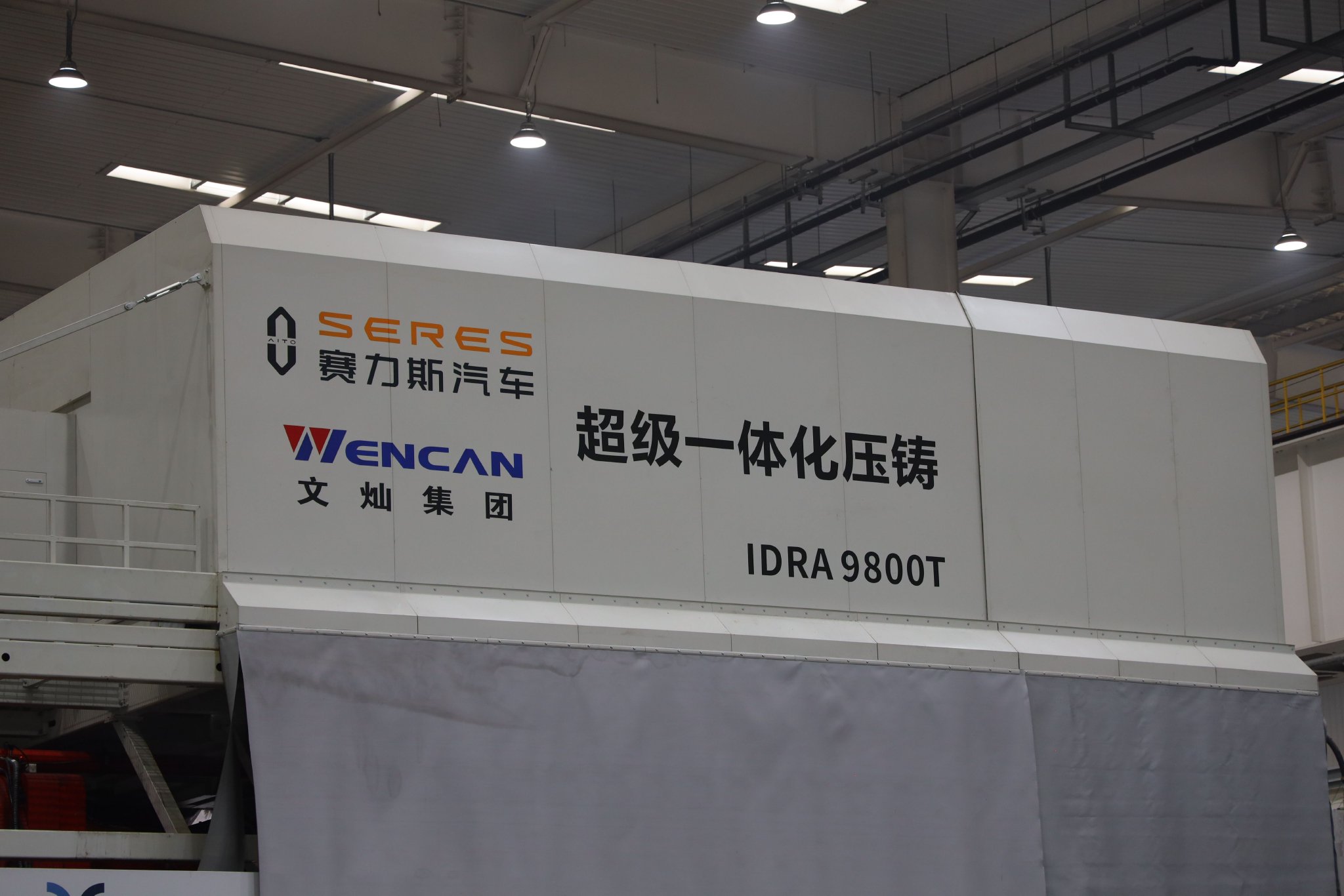
另外,“锁模力”越高,成品率越能保证。压铸技术是通过压力将高温液体金属压入模具中的,如果压力不够高,液态金属流速不够快,可能流不到模具末端就凝固了。所以,压力越高,液态金属流动的越快,越能在凝固前更快地充满整个模具。这就是为什么一直要强调“锁模力”,也就是常说的吨级。
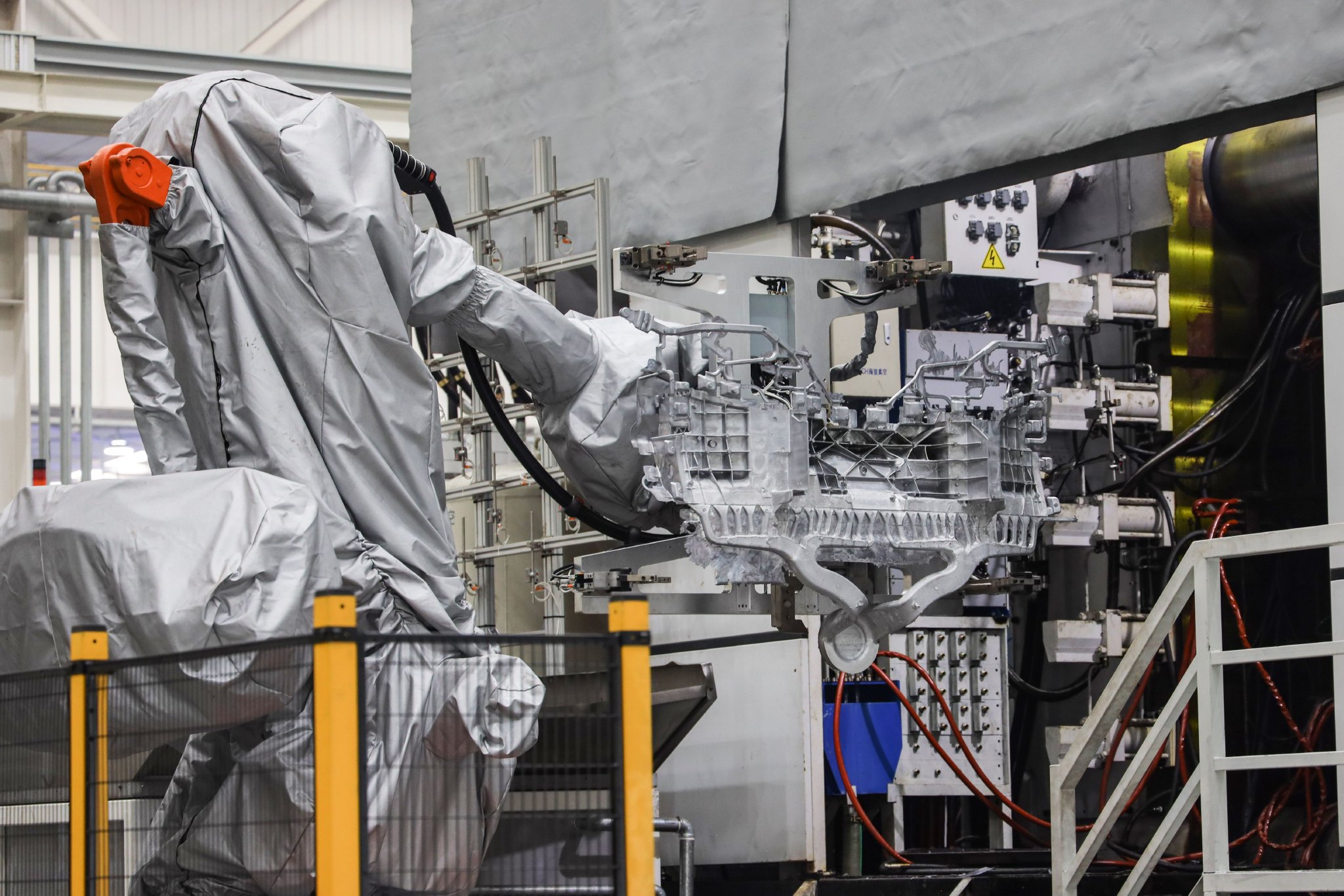

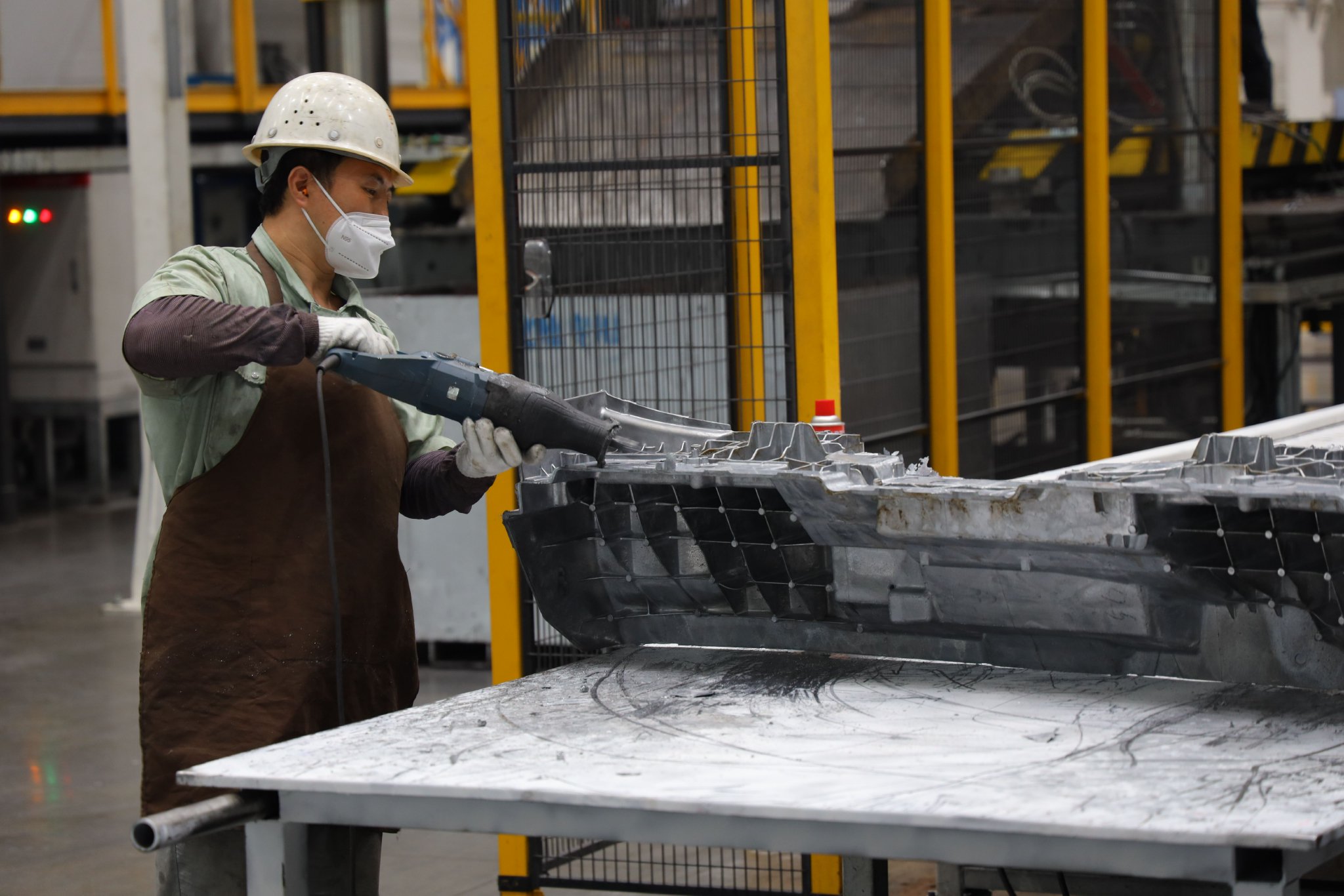
从现场来看,从进料、压铸、产出压铸件、修正压铸件到初步成品,用时2分钟左右,而且整个工位只有三位工人,生产效率非常高。如果是传统冲压+焊接工艺,一个大型部件就需要在生产线上“走完”1个小时时间。
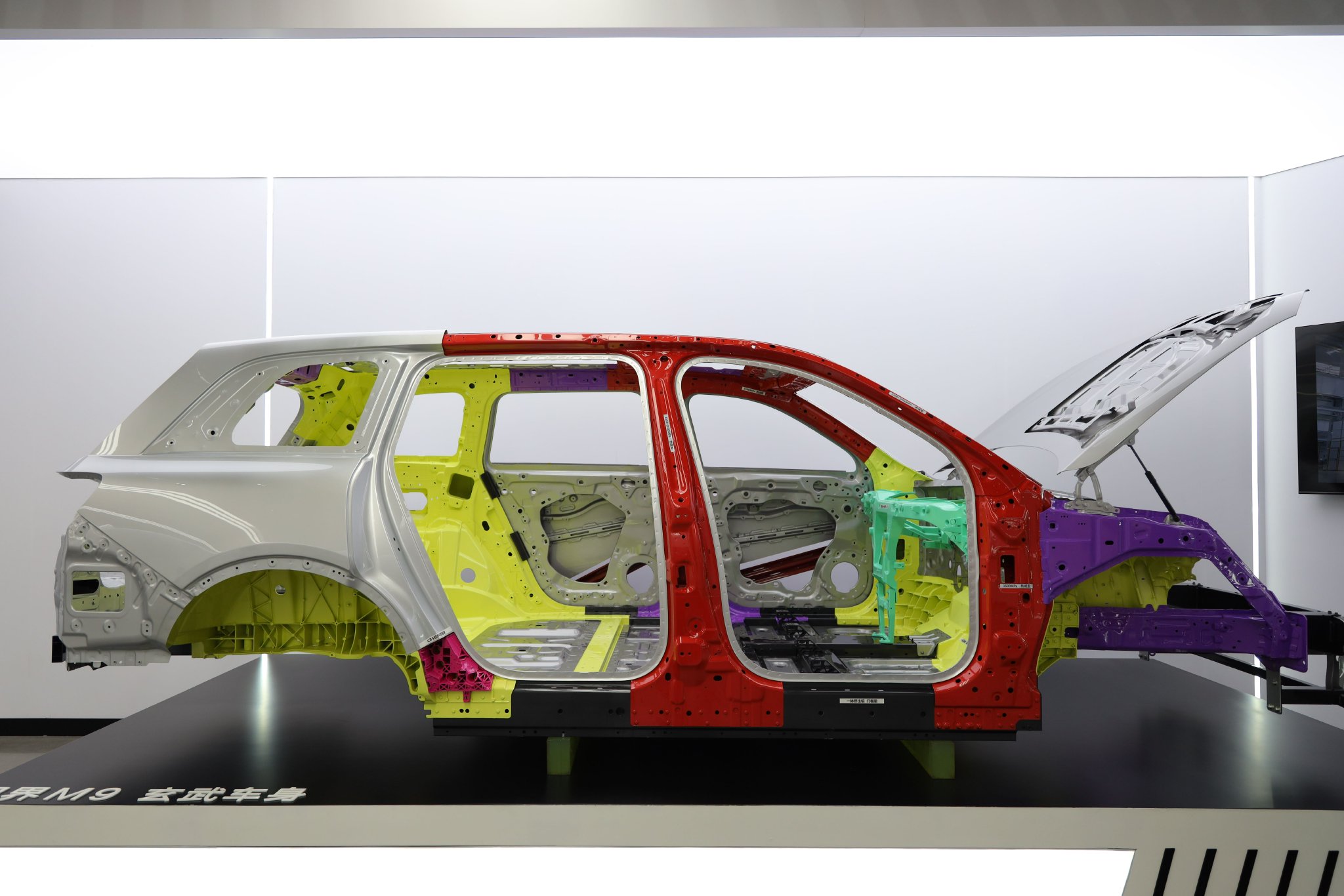
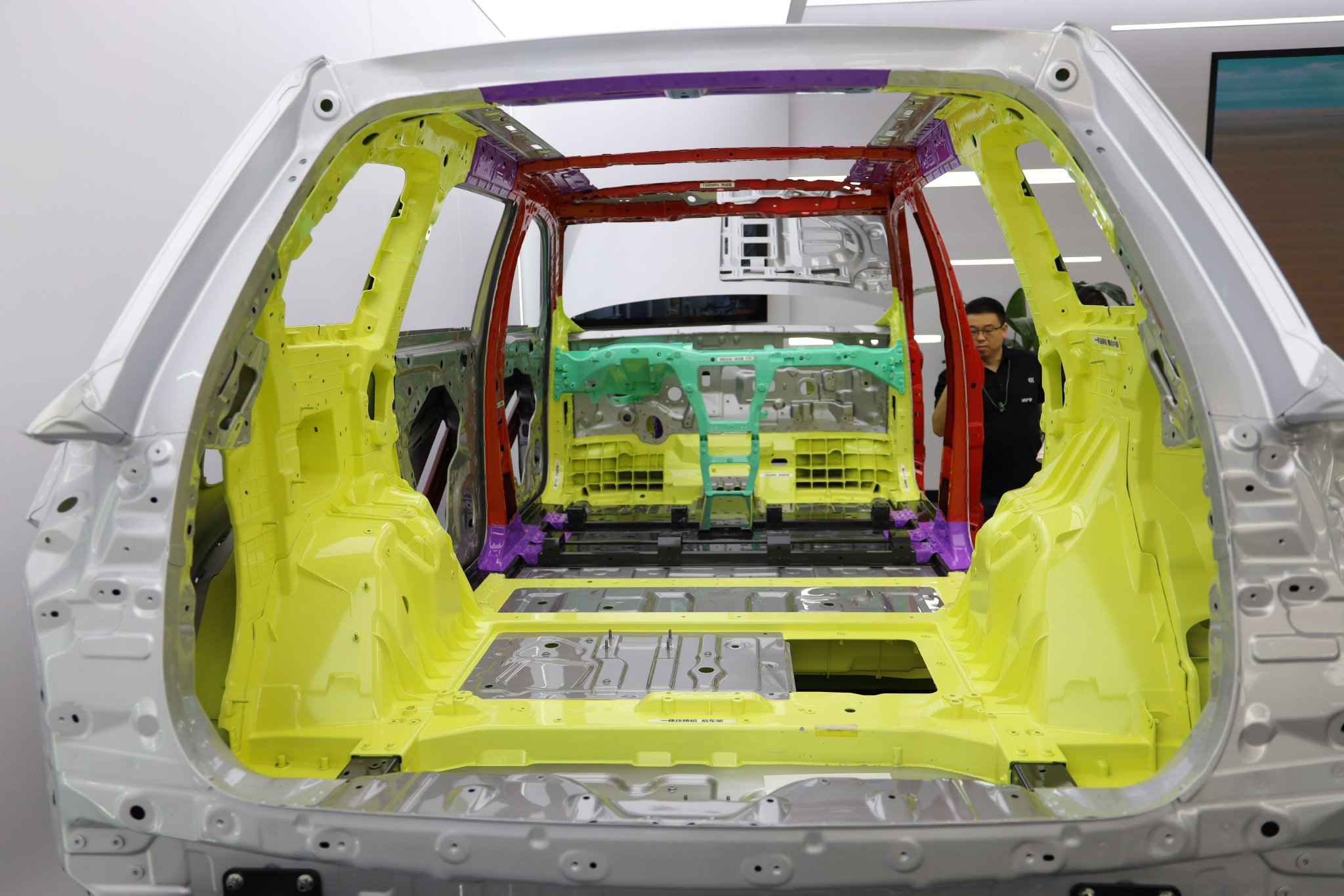
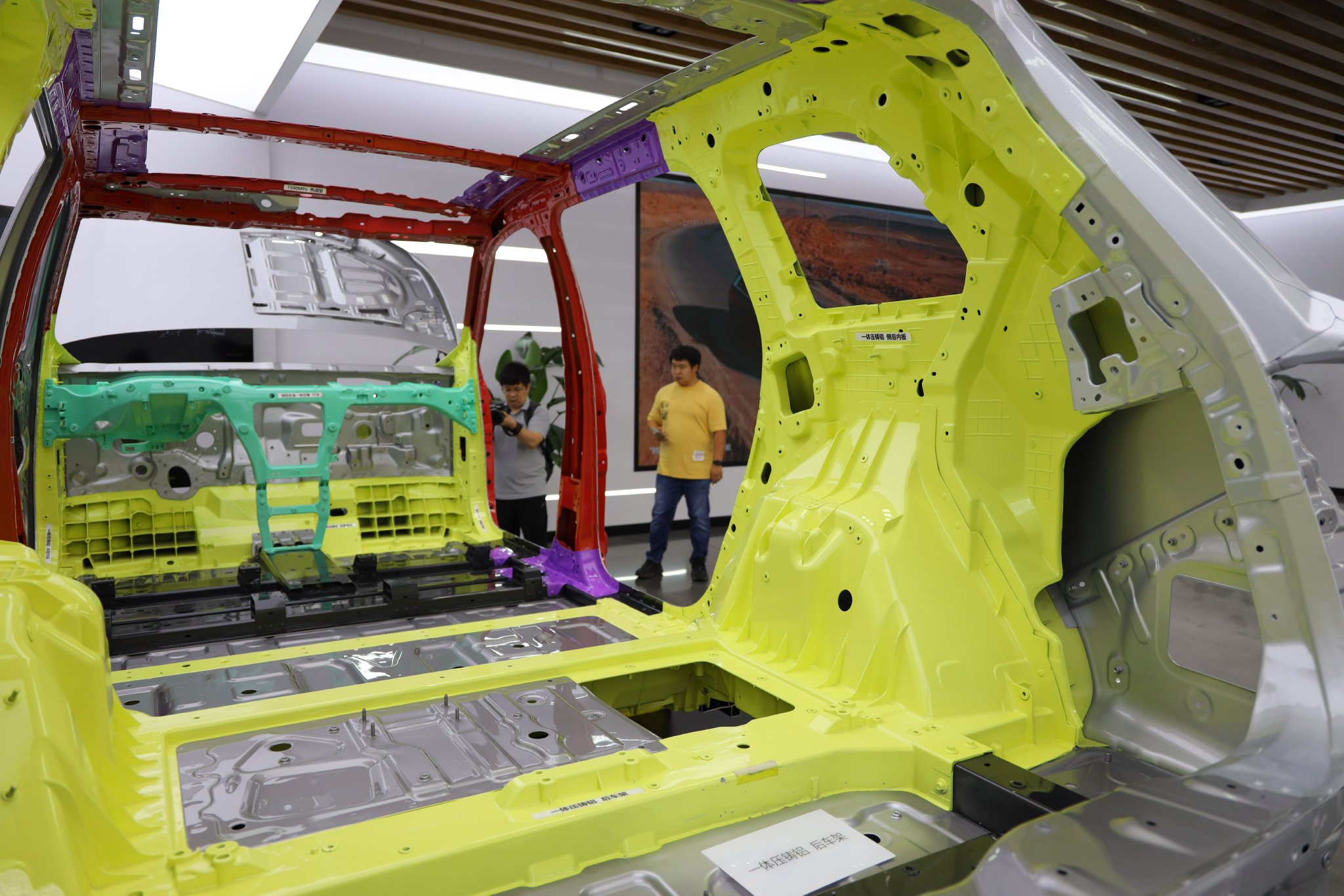
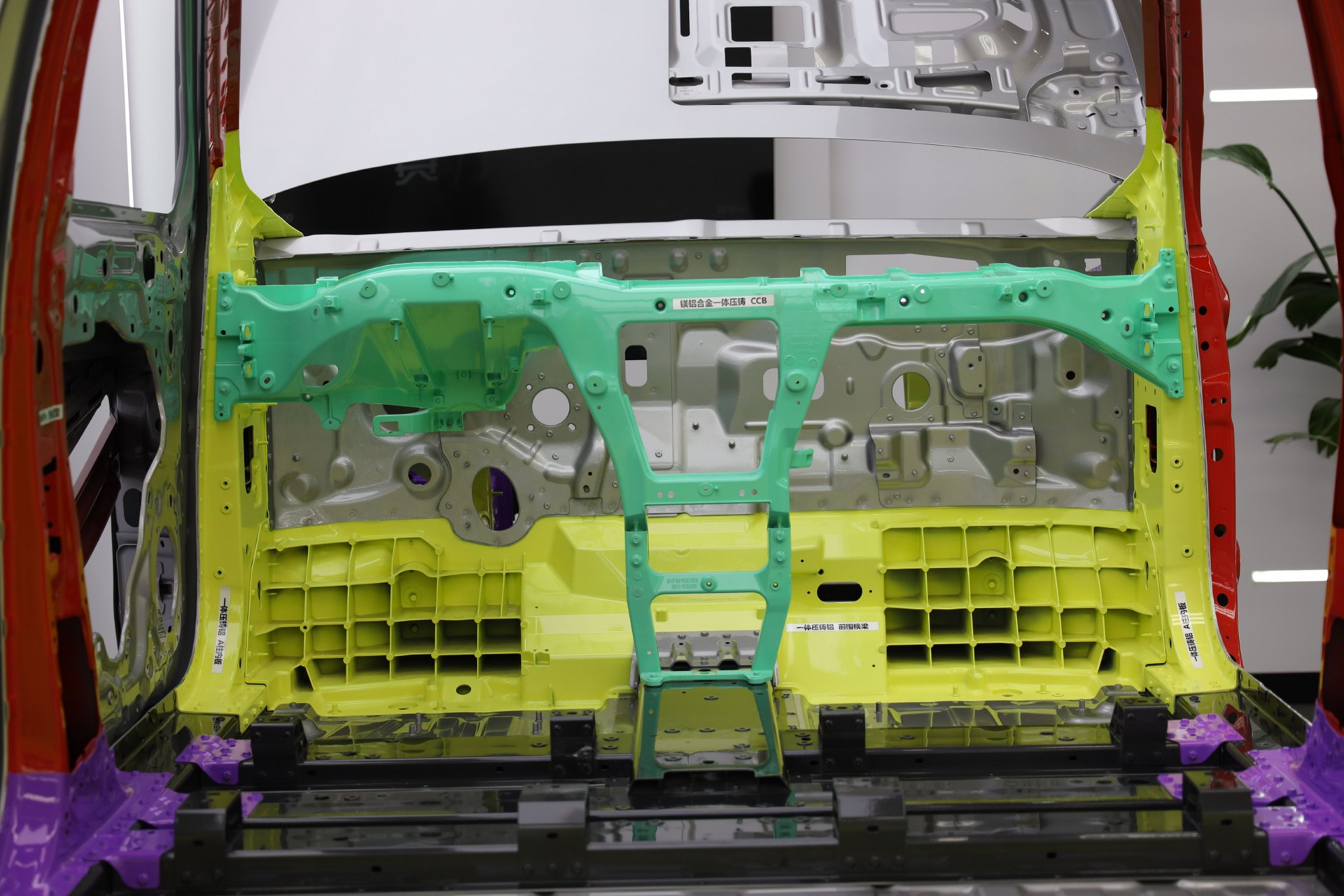
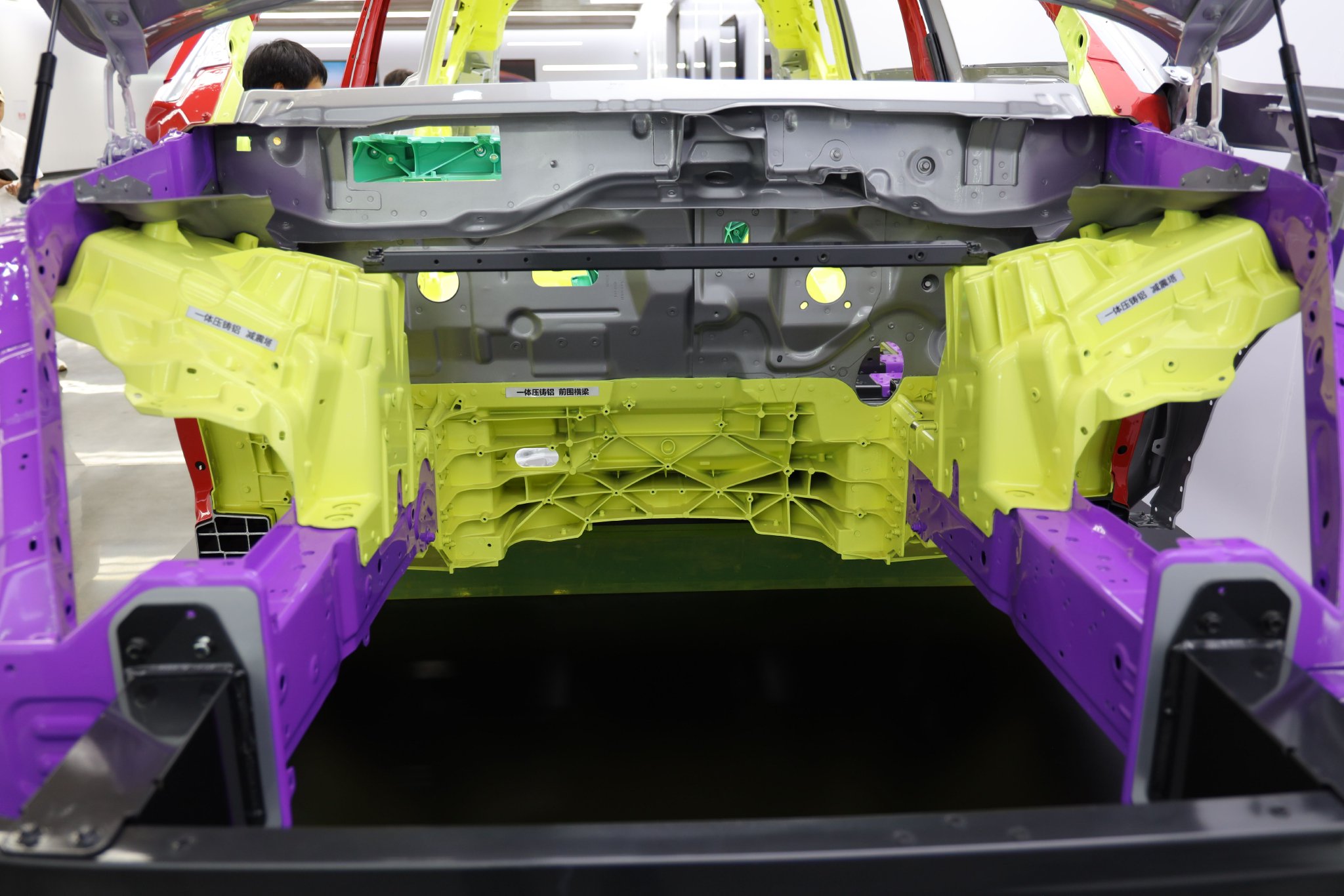
对于车辆来说,压铸车身可以使得车身轻量化。一体化压铸技术通常使用铝合金材料,有助于减轻车身重量,从而提高新能源汽车的续航能力。还可以提高安全性,一体化压铸车身减少了大量焊点,使得车辆的整体结构拥有更高的强度和抗扭转刚度,提高了车辆的安全性。另外,还可以增加空间利用率,由于电池通常平铺在车底下,一体化压铸技术可以更有效地结合车身与电池,从而增加车内空间。
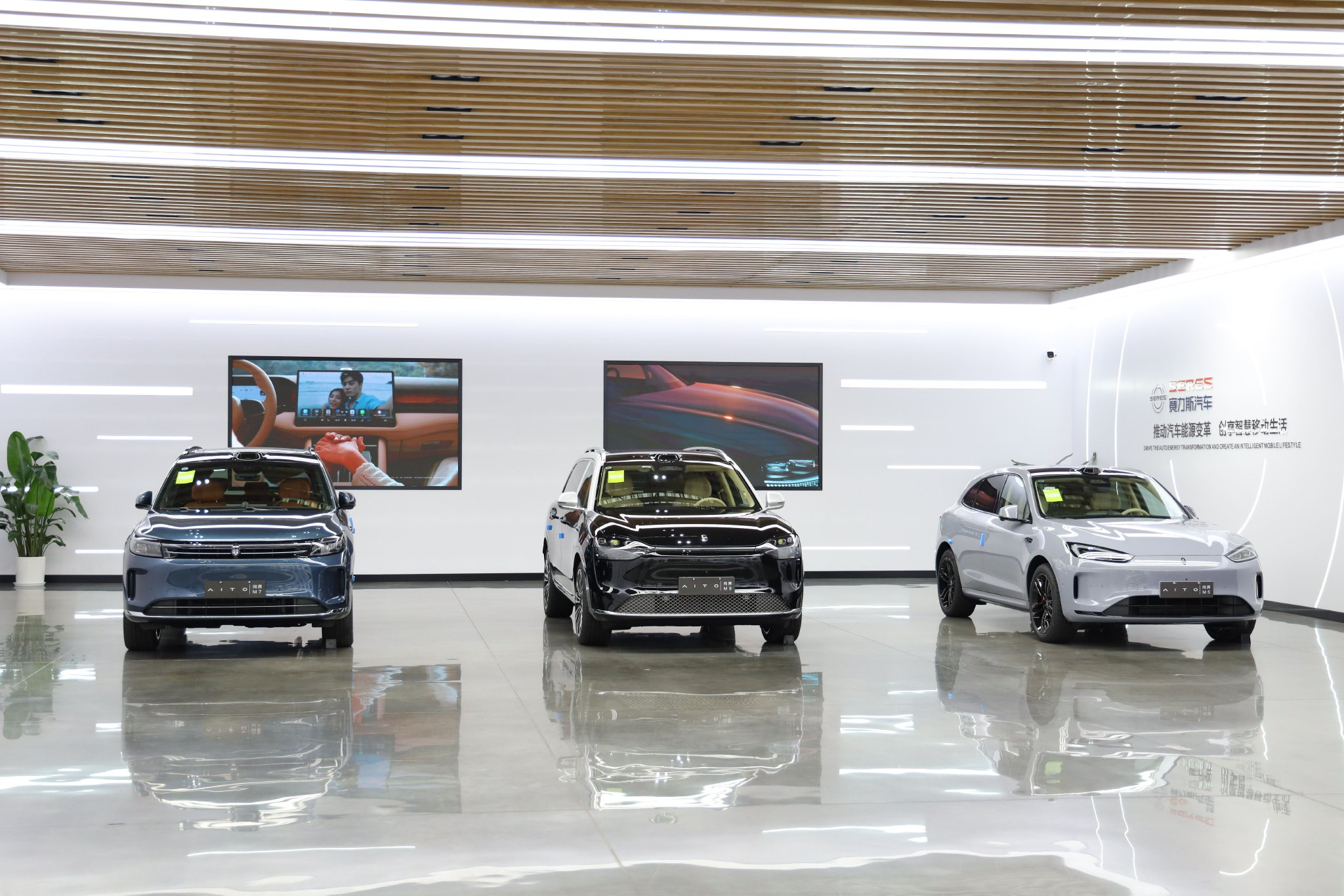
而对于消费者来说,压铸车身可以降低整车价格。由于生产时间和成本的降低,为整车价格的下降提供了空间,从而降低整车价格让消费者受益。
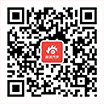
更多汽车资讯,涨知识赢好礼扫描二维码关注(auto_sina)