规模为什么有时不经济?
汽车工业是典型的规模经济,但是由于各种原因,中国汽车工业的发展并没有给规模经济添彩,相反却使人怀疑规模经济到底是否有效。提倡规模经济的目的,是为了降低生产成本,从而提高经济效益。企业经济效益主要取决于生产成本和产品销售价格的关系,而扩大规模只是降低成本的途径之一,因此对规模经济要有深入的认识。
市场的规模是生产规模的前提
产品的社会需求是确定企业生产纲领的第一个因素,也是生产规模的决定因素。一般地说,产品的社会需求量越大,其生产的经济规模也就越大。对汽车来说,各类汽车的社会需求量是不同的。轿车的社会总的需求量非常大,尤其是普及型轿车,必须是较大的规模才能满足社会的需要,所以,世界上普遍认为轿车厂经济规模一般在20—30万辆。轻型汽车的社会需要量次于轿车,但是大于重型车,其经济规模在10万辆左右。重型车的社会需要量相对较少,而且总吨位越大,经济规模越小,一般在5万辆以下。
市场规模与成本的关系,是互为前提的。市场决定规模,规模决定成本。但是,反过来说,成本也决定市场。汽车诞生的头几十年间,只不过是富贵人家是高级玩艺儿,是身份的标志,这是因为当时汽车的价格昂贵,一般人不敢问津。自从福特发明T型车以后,汽车才成为普通人的交通工具,在社会上普及开来。福特以大量生产的方式降低了汽车的生产成本,取得了经营上的成功。一般流行的看法,是“大量生产就会有低的成本”,但是有人在研究了福特的生产体制以后,认为这种说法应该倒过来说,即:没有低的成本就不可能实现大量生产。这是因为大量生产的一个前提条件是要以市场的需要来考虑规模。福特之所以创立大量生产的体制,是因为他预测出以五百美元的价格可以销售出数百万辆车;而他之所以敢将价格定在五百美元以下,是因为他设计的装配线可以使成本大大降低。所以,大规模生产是福特采取低价政策的结果,而不是它的原因。
美国《哈佛商业评论》曾经刊登过一篇论行销的文章,认为“大规模生产的产业中常有一股不可抗拒的倾向,迫使他们尽可能多的生产。大规模生产可使产品的平均单位成本显著降低,很少有公司能抗拒得了这种诱惑。”“以汽车工业为例,它向以大规模生产著称,业者也以此为荣,而对整个社会的冲击亦相当大。该产业每年要提出新车型,才能保证其兴隆不衰。他们的策略也必须是顾客导向。”
一个汽车厂的经济规模不可能以一个单一的汽车产品品种来实现,这是由于市场的竞争,迫使汽车生产厂努力适应用户的多方面需要,这就需要增加产品品种。
英国的约翰·哈特利认为,“为了在产量方面竞争,一个汽车制造公司至少要有面向不同销售领域的三种基本车型:诸如微型、超微型、轻型、中型和大型。”当然,还包括在各个级别的车型下,众多的变型车。“这有助于增加总产量,也有利于把人们吸引到产品陈列室去。”(约翰·哈特利《汽车生产的经营管理》)
成本的降低不仅仅取决于规模大小
同样的产品,随着企业规模的不断扩大,其成本不断降低,这就是规模优势。马克思在《资本论》第一卷中指出:“大规模集中的共同使用的生产资料的价值,一般地说,不会和它的规模和使用效果按比例增加。由共同使用的生产资料转移到单个产品中去的价值部分所以会更小,一部分因为它所转移的总价值,要同时分配到较大量的产品中去,一部分因为和分散的生产资料比较,它加入到生产过程中去的价值,绝对地说固然较大,但是考虑到它的作用范围,相对地说,却是较小。”
英国的乔治·马克西和奥布里·西耳伯斯通在《汽车工业》一书中提出了一条著名的汽车产量与单位产品费用之间关系的曲线:
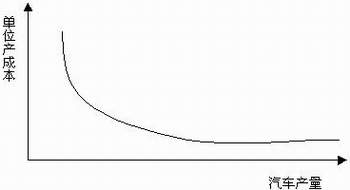
这条曲线是在研究规模经济时被一再引用的论据之一,在论证中国汽车工业经济规模中也是“砫石”性的论据。两位教授是以50年代英国汽车工业的实际情况为基础分析得出的结论。他们在《汽车工业》一书中说:“在生产规模扩大的初级阶段,厂家取得的节约效果最大,年产量从1000两增加到5万辆时,成本可望下降40%。年产量翻一番,达到10万辆时,成本下降15%。产量再提高一倍,为20万辆时,可进一步节约10%。跃升到40万辆时,又在进一步节约5%。超过40万辆,产生的节约效果急剧减低,大体到100万辆水平时,已经不再有节约效果。”
马克西和西耳伯斯通曲线影响很大,但是后来许多学者提出了不同的看法。日本影山僖一《现代汽车产业论》一书中指出:“制造成本根据种种重要因素而变化,如材料的价格变化,工资的变动,材料费、劳务费节约以及因使用新、尖设备而提高的劳动生产率,技术进步等重要因素。由于大量生产带来制造成本的下降,这只是每辆车制造成本降低的重要因素之一。”马克西和西耳伯斯通曲线没有考虑采购和劳务费用的变化影响。“产量是获得规模经济效益时的手段,若要使产量能达到经济规模需要几年的时间,设备能力也要扩大,生产供应方面的条件也要大幅度变化。若要从一般产量过渡到实现经济规模的转折点,需要几年的时间和大量的投资。若要达到年产20万辆、40万辆甚至80万辆的产量,则需要较长的时间和巨额的投资。”
日本影山僖一对1956年到1977的日本汽车生产成本进行了计算,根据他的计算资料对单车成本进行计算,可以发现日本汽车工业单车成本并不是随产量扩大而直线下降,反而出现上升趋势。(见图)主要是因为材料和人工费用不断上涨,特别是石油危机以后,原材料和零部件采购费用都明显上升。

不同工艺有不同的经济规模
汽车工业生产的各种工艺方法由于加工性质不同,所需要的经济批量也是不同的。日本《汽车工业手册》对汽车工业几种主要工艺方法的经济规模提出的数据是:
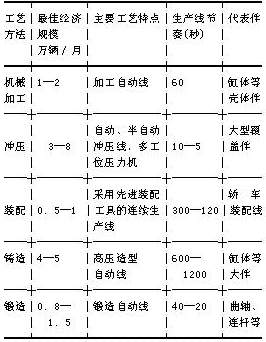
⑴机械加工
机械加工的经济规模取决于设备的加工节奏。对于自动生产线和流水作业线来说,取决于设计节奏。加工节奏受切削规范、设备动作时间、加工量的大小等条件的限制。一般情况下,自动线的经济规模大于流水线,流水线又大于通用设备。
⑵冲压
冲压设备生产效率都很高,目前最高水平的冲压自动线每分钟行程次数可达12次,节奏为5秒,按一线一件计算,年产可达百万件以上。但是由于冲压生产总是以批量方式进行,所以经济效果最好的产量并不是它可以达到的最高产量,因为更换模具要占用一定的时间,另外按照“水桶理论”,系统的最高能力取决于其最低环节,冲压生产要和其他工艺相平衡,这就限制了冲压自身的经济规模。
在日本,采用专门设备和改进操作,使得更换模具的时间由一般的数小时降低到15分钟,这样可以采用较短的换模间隔,使冲压加工的经济规模更加接近它的理论最高产量,以较少的设备生产全部冲压件。
⑶焊接
从理论上说,焊接是一种连续作业,但是由于车身是由若干分总成组成的,如地板、前围、侧板、车门、覆盖件等,这些分总成结构不同,分装工艺很少能连续进行。在采用机器人的焊接车间里,焊接的连续性得以较好地实现,年最佳产量可达到30万辆份。自动多点焊机的节奏为0.6—2分钟,年产规模可达10—30万辆。对于手工焊接,规模则小得多。
⑷铸造
以气缸体铸造为例,年产量10万辆已经合算,国外有的工厂达到85—100万台份。但是铸造的投资在汽车工业全部投资中的比例最大,需要巨额资金,特别是自动铸造线,这就制约了铸造的规模。
⑸锻造
锻造生产设备的效率仅次于冲压,但是由于批量生产和模具寿命的限制,不可能实现连续生产,它的经济规模不是很高。有的厂商为提高效率,采用以铸代锻的方法。
⑹装配
在汽车生产中,装配的手工作业程度最高,在单位产品所需工时中,装配工时占40—50%,在各种工艺中,装配的经济规模最小,数万辆就可以得到较好的效果。另外,装配线的节拍不能短于1分钟,因为装配属于简单重复劳动,劳动强度大,动作频度高,容易疲劳,时间过短,工人难以接受。
作为汽车厂的规模,要在各种工艺经济规模之间进行平衡,才能达到整体的经济规模。
对某一种工艺方法来说,由于生产方式不同,其经济规模也就不同。各种生产方式都有自己的经济规模。以机械加工和冲压为例:
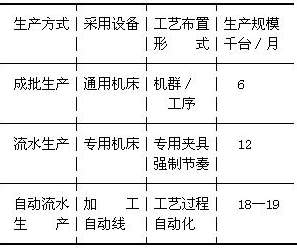
冲压工艺的主要生产方式及经济规模
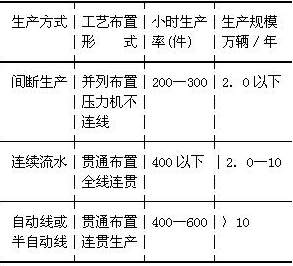
技术进步有两个方向—自动化和柔性化。这两个方向都可以提高劳动生产率,降低成本。
自动化的结果,使得设备的生产率越来越高,专业性越来越强,生产规模越来越大。
柔性化对经济规模的影响比较复杂,有多种情况:
对于专用生产线来讲,柔性化使得生产线的灵活性增强,可以通过两种以上的产品,但是生产线的加工节奏不变,所以一般不会改变自动线的经济规模。
对于通用生产线,柔性化技术使得模具、刀具的更换时间缩短,减少了不同品种生产的中间调整时间,提高了设备的利用率,因而可以缩小经济规模。
目前,世界上发展很快的柔性生产体制(FMS),包括柔性加工系统和弹性工作系统,具有灵活多变、多品种生产适应能力强的特点,使得加工的经济规模较大幅度地减小。
应该指出,柔性化的主要目标,是增强生产的灵活性和市场的适应性,提高效率,减少人工费用,从而降低成本,而柔性化本身,是需要增加投资的,它的经济性必须以提高效率来补偿。总的来看,技术进步的结果,提高了资本的有机构成,减少了活劳动的消耗,所以说,有的技术进步扩大了经济规模,有的技术进步缩小了经济规模。
从第一利润源发展到第三利润源
从福特生产方式到丰田生产方式,主要是在生产制造领域降低成本。福特的做法是加大生产批量,把固定费用摊薄,甚至成倍增加工人工资的情况下仍然能降低产品制造成本。福特生产方式之所以能取得成功,主要是当时汽车价格较高,降价空间比较大;其次是市场需求量大;第三是在汽车普及初期对性能、舒适、美观方面要求不高。
日本汽车工业面临的是一个比较狭小的市场,同时消费者对品种、质量的需求也提高了,无法采用福特生产方式,因此出现了丰田生产方式。丰田生产方式的核心消灭生产环节的所有浪费,比如取消中间库,实行看板方式,按照需要量生产;减小订货批量,增加订货批次;实行标准作业,减少无效动作。丰田生产方式不仅减少资金占用,还可以减少生产面积,减少生产工人,减少建设资金,并减少人工费用。
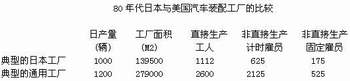
80年代开始,大众公司开始向第二利润源――采购压榨利润,这就是全球采购、产品平台战略、模块化生产。全球采购本身没有什么了不起的,只不过把比价采购方式推广到世界范围,但是模块化生产却改变了汽车工业的面貌,由于制造又苦又累又不赚钱,因此现在的汽车制造商把越来越多的工作量推给了零部件企业,以至于有人预言,现在的汽车制造商最终会成为品牌所有者,那时为数不多的零部件制造商将为全球的汽车公司定牌生产。模块化方式可能使整车装配所需要的最低经济批量下降,因为零部件供应商是面向全球来供应模块的,他的批量非常大。
平台战略一方面用减少底盘数量的办法来压缩总的开发费用,但是另一方面却需要以更大的产量规模来摊掉开发费用,一个平台需要100万辆以上的产量规模。
有的研究表明,在现代化大生产中,产品生产的直接成本不断降低,而流通费用的比重却在持续上升。工业品在全部生产过程中平均只有5%的时间是处于直接加工制造过程,其余95%都处于搬运、储存状态,流通费用占到全社会物质生产的三分之一左右。由于管理科学的长期发展,在生产领域节约劳动力和原材料已经比较困难,而过去被人们忽视的物流方面节约的潜力还很大,因此在日本被称为“第三利润源泉”,美国称之为“成本经济的最后领域”。
物流有两种含义:物的流动和物的流通。就一个工厂内部来说,物的流动包括供应物流、销售物流、生产物流。生产物流基本上发生在工厂内部,属于生产领域中物的流动;供应物流和销售物流发生在流通领域,属于流通领域中物的流动,也可以成为物的流通。流通领域的物流包括货物运输、装卸、包装、仓储管理、订货和发货、市场预测、客户服务等(荣朝和《论运输化》)。
物流的内容早就存在,但是物流的概念和物流管理出现于50年代。随着工业化和经济发展的进程,人们对物流的认识和组织物流的方式发生了很大变化。初期是以改善硬件为主,如大型物流设施的建设、集装箱运输的发展、高等级公路和卡车运输的普及、机械装卸和传输、立体自动仓库、自动分拣系统等,提高了物流系统的能力与效率。70年代以后,发达国家在开始注重改善物流的软件,强化物流管理,企业开始在整个经营组织中考虑物流活动,着眼于建立一种新的物流秩序,重新组织物流体系,提高物流效率,采用计算机管理和信息网络技术,以适应现代经济发展的需要。
运输业完成货物的位移,归根到底是社会经济中物流过程的组成部分,在运输化尚未完善阶段,运输业没有充分发展,经济增长特别依赖于社会总位移能力的增加,因此运输的地位比较突出。随着现代运输体系逐渐成为经济运转的良好条件,物流管理的地位就突出出来,运输业则逐渐转化为适应社会生产对加快物流速度的需要。现代经济的突出特点之一就是运转速度越来越快,生产的社会化程度越来越高,对运输系统提出了效率和质量方面的更高要求。物流管理是运输化发展到一定阶段的必然产物。根据“日本货物纯流动调查”资料,从1975年到1982年,日本物资批发中心订货总量增加了27.5%,每批的订货量却下降了43%,要求当日到货的紧急订货增加了73.3%。日本丰田公司发明的“丰田生产方式”或称“及时化”生产,对供应物流更提出了“准点供货”的要求。这些都代表了物流需求的新变化。
从第一利润源到第三利润源,降低成本的天地非常广阔,绝对不是一个规模便了得的事。(贾新光)
订汽车新闻短信把握汽车时代先机        新浪企业广场诚征全国代理
|